基于熔覆-挤压工艺的100MN/300MN/1200MN第三代液压机及产业化项目可行性报告
时间:
2017/4/10 19:58:55
浏览量:5218
基于熔覆-挤压工艺的
100MN/300MN/1200MN
第三代液压机及产业化
项目可行性报告
《详细摘要》
一、项目的背景简介
二、三代模锻液压机
三、熔覆工艺与熔覆-挤压工艺
四.项目市场分析
五.项目简介
六.项目实施
七.团队已有成果
八.附件1
九.附件2
《详细摘要》
《基于熔覆-挤压工艺的100MN/300MN/1200MN第三代液压机及产业化》项目(简称《熔覆-挤压》项目)
,将3D打印的激光金属成形工艺的LCD——laser cladding deposition工艺,即激光熔覆沉积制造工艺,与现代垂直分模挤压相集成,形成一种全新的重型金属成形制造工艺,即先用LCD制造毛坯,再采用重型挤压完成最终成形,称为CE——cladding extrusion工艺方法,即熔覆-挤压工艺。CE工艺是用于高端结构件制造的先进成形工艺,是为我国本和世界的航空、电力、高铁、海洋、核电和军工(包括潜艇结构件、导弹、鱼雷、火炮等)服务,为我国转向创新型社会的转型升级服务的重要工艺。本项目,在统一规划下,研制和分期开发制造100MN(一万吨),300MN(二万吨)和1200MN(十二万吨)三台世界级的,执行熔覆-挤压功能的,第三代模锻液压机——垂直分模挤压液压机及相应的辅助设备,并配以4台重型结构金属熔化成形设备,形成节约材料、降低能源消耗、减少排放的现代金属成形制造生产力。
本项目提出垂直分模挤压工艺,它具有三大优点:
(1)与传统的挤压工艺相比,可完成更为复杂结构件。它将挤压模具剖分左、右两部分,经强大的水平力结合为密闭的挤压腔,通过挤压头挤压金属而成形。完成挤压后,左右分开可取出十分复杂的挤压件;
(2)与闭式模锻工艺相比,节能20~50%。垂直分模工艺将锻件的最大截面,作为分模面而垂直放置(垂直分模工艺之名称由此而来),与垂直载荷平行,承压投影面积大大下降,则节能;
(3)与模锻工艺相比,充型能力成强,成形精度高。不是通过模壁迫使金属流动,而是通过挤压头的挤压,来充满型腔,可完成细小圆角的成形。
本项目将垂直分模挤压工艺与LCD(3D打印大家族的金属成形工艺)相结合,形成熔覆-挤压工艺,即CE——Cladding Extrusion工艺。利用采用金属粉末在惰性气体保护下而成形:实时将金属粉末送到数千瓦激光束聚焦的焦点上,粉末熔化形成微熔池并快速凝固和组装成CAD模型所规定的结构。CE技术两大特点:
- LCD的粉末在微熔池(数十微米至数毫米)中熔化并组装成形,不存在大体积液态金属体(数吨至数百吨)在凝固过程中固有的成分和杂质偏析(不均匀分布),故采用LCD毛坯,因成分均匀而无需开坯,节省大量的设备、资金和时间。无需重型钢锭和铸坯,也就节省了重型冶炼、真空浇注一系列重型装备。这一优点对重型制造来说,是革命性的。
- LCD的优良成形性,为后续的重型挤压提供形状最合理的毛坯,使挤压工艺的挤压力下降,挤压模寿命提高。
CE工艺是先进的垂直分模挤压工艺与先进的3D打印工艺相巧妙结合的典范,
本项目规划3年建成:第一期分别投入2000万和6000万,第一期启动后一年内分别完成,以4台YLC-2熔覆设备和100MN压机为主的分项目,产值2000万/年;第二期投入1.3亿,第一期启动后三年内,300MN压机投产后,产值达2亿/年;第三期投入6亿,第一期启动后4.5年内 1200MN压机投产,产值达30~50亿/年。整个项目需8.1亿。以上投入和产出为初步计算,根据项目的深入和市场的变化,将可能有小幅调整。
一.项目的背景简介
进入21世纪,重型、大型和具有壳台、管台的复杂腔体等于核电、海工和军工高端结构件的质量要求越来越高,数量要求越来越多。一般锻件卖不动,高端锻件供不应求,现在是“谁有核锻件,谁就有核电站”的年代。传统的重型自由锻设备在我国十分过剩,但又解决不了高端锻件的问题。自由锻造精度很差,材料和能源浪费很大、制造周期很长。一吨零件平均需8吨钢锭,大量的材料被浪费掉了。一根重量8-10吨的核电一回路主管道零件,需一年的制造周期。钛合金空-空导弹弹头和弹体的材料利用率小于50%。核锅炉锻件(508-Ⅲ钢)之钢锭利用率仅为20%-25%。
上述问题采用重型模锻和多向模锻也无能为力,前者适用于航空壁钣和杆件,后者适用于小孔腔体件,无法解决和弥补自由锻的先天不足,根本解决不了重型、大型和具有壳台、管台的复杂腔体高端锻件。
我们的时代已在强烈呼唤新的塑性成形技术、工艺和设备:全世界都需要一种既能像自由锻那样高柔性(无需专用模具)的重型数十吨至数百吨锻造锻件之锻造工艺;又能达到模锻和挤压的精度和效率。本项目在本团队数万吨重型模锻、多向模锻液压机和重型挤压工艺和装备成果的基础上,提出重型垂直分模挤压工艺和设备并将其与重型熔覆成形工艺(一种激光金属3D打印工艺)相结合, 行成一种全新的,高端的,节材和节能的高效率的重型金属成形工艺和设备,它开辟了一个重型装备制造的新时代。
二.三代模锻液压机与垂直分模挤压液压机
本报告将重型模锻液压机分为三代:
第一代模锻液压机为水平分模单向锻造液压机,执行水平分模开式/闭式模锻工艺,这是适应航空大型壁板件批量生产的需要而发展起来的重型液压机。重型自由锻液压机,根据水平分模平砧/型砧锻造的原理,显然,自由锻液压机属于第一代模锻液压机。
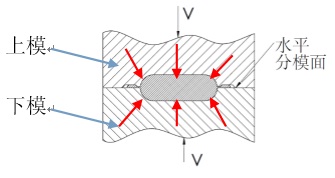
图1水平分模模锻图
所谓“水平分模”,是指上模和下模在水平的分模面上合模(图1),通过型腔的模壁对坯料施压,并约束金属流动而成形。为了利于金属充满型腔,必须必需使模膛最浅,这就形成了以锻件的最大截面为水平分模面,因而承压面积最大,模锻的球应力难以提高,充型能力受限。此外,上下模具互相压靠,以及毛边的承压,都吸收了大量的能量,充型能力受到进一步影响。
第一代模锻液压机没有垂直挤压功能,一般也没有垂直穿孔能力。以大型壁板类、平面框架类和杆类锻件(一、二维结构)为代表的航空高端锻件是主要产品,其工作台面很大,相比之下,净空高、行程和立柱间距均不很大;
第二代模锻液压机为多向模锻液压机,见图2
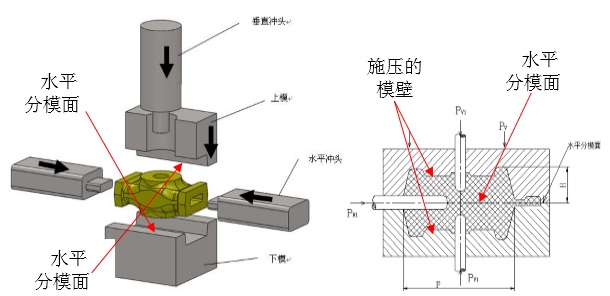
图2 多向模锻示意图
在第一代水平分模的模锻压机的基础上,增加水平穿孔针(冲头,穿孔力达到垂直压力的20%), 即成为第二代模锻液压机——多向模锻液压机。需强调指出,二代液压机锻件的的分模面仍然是水平面,成形主要还是靠模具的模壁施压,穿孔针(冲头)起辅助作用。石油泵、阀、通体等厚壁腔体(3维厚壁腔体为主,壁厚与腔体内半径之比接近0.8~1.0)等复杂锻件是二代机的主流产品。
上述第一、第二代模锻液压机将锻件水平放置(锻件最大截面垂直于液压机的主载荷),主要依靠模膛的,接近水平状态的腔壁压制金属而成形,此种推动金属流动的方式,用于腔体薄壁化、尺寸精化和结构一体化(壳-台和管-台一体化)的21世纪高端锻件,问题很大:成形过程的充型能力不够,材料变形的热-力过程强度不够(球应力不够大)、应力分布不均匀,变形能量不能有效利用。
第三代液压机为垂直分模挤压液压机,改类液压机执行的垂直分模挤压工艺,它是在多向模锻和挤压工艺基础上发展起来的新工艺,在我国尚鲜为人知。为保证复杂件的挤压成形,将挤压筒(模)剖分为为左模和右模,形成垂直的分模面(在强大水平力H(可达垂直压力V的50~60%)的支持下,左、右模在垂直的分模面上合模,形成封闭的闭式型腔,为挤压创造了条件。见图3、图4。将分模面转90度,锻件垂直放置,也转90°,模膛深度也就不会增加,与第二代液压机多向模锻相反,此处是锻件的最小截面承受垂直主载荷,在封闭型腔中,挤压头(冲头)将主载荷直接施压于变形材料,而不是型腔模膛壁施压,这种挤压性质的施压,垂直主载荷V得到最大程度的利用,这样可获得最大的球应力(可达500Mpa以上),应力分布更均匀,金属的流动是独立的冲头挤压金属而成形,具有最大的充型能力(可充满细小的缝隙和圆角)由于挤压型腔可合可分,因而可完成十分复杂结构件的挤压,是一般挤压筒(模)无法比拟的,是成形复杂的轴对称或非轴对称,大尺寸,薄壁腔体(壁厚与腔体内半径之比接近0.1~0.3,甚至更薄)的现代利器。
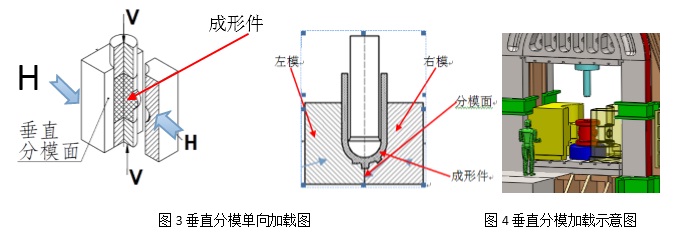
垂直分模压机最早出现在美国德州的ETF(Ellwood Texas Forge)公司,这是成立于1910年ELLWOOD集团的下属的高端模锻锻件生产专业厂商,于上世纪80年代左右推出了世界第一台1.1万吨垂直分模模锻液压机。图5为该压机锻造的实景照片,垂直分模面、挤压头和穿孔针清晰可见,永年公司拥有垂直分模挤压、分布挤压工艺和相应设备的国内外专利。
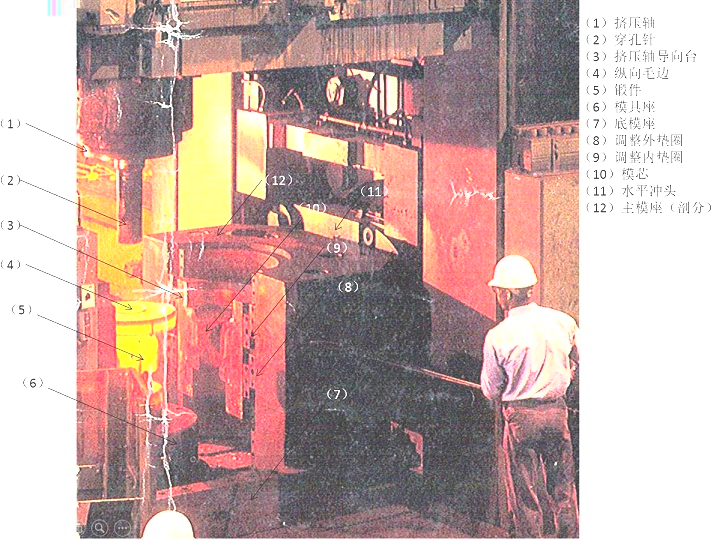
图5 美国ETF的110MN生产的产品照片
三代模锻液压机比较表 表1
|
第一代液压机(航空模锻压机) |
第二代液压机(多向模锻压机) |
第二代液压机(垂直分模挤压压机) |
分模方向 |
水平分模 |
水平分模 |
垂直分模 |
施压方式 |
模壁施压 |
模壁与挤压混合施压(模壁施压为主,穿孔针挤压为为辅) |
纯挤压方式(挤压轴挤压和穿孔针挤压) |
水平力/垂直力(H/V) |
0 |
0.2~0.25 |
0.5~0.6 |
能量利用率 |
低 |
较低 |
高 |
压力利用效率 |
低 |
较低 |
高 |
充型能力 |
低 |
较好 |
最好 |
成形球应力 |
低 |
较低 |
高 |
应用 |
壁钣及杆件 |
小孔中空结构 |
复杂大孔中空结构 |
第三代液压机是挤压工艺、多向模锻工艺的进一步发展,是金属成形制造重型装备领域的突破性进展。垂直分模挤压工艺与《分布挤压》、《旋压工艺》结合起来,可完成更大尺寸的核反应锅炉的水室封头、导弹弹体和弹头、潜艇部件、重化工超大型封头等。第三代液压机的功能能完全可以覆盖了第一、二代液压机的功能。
第三代液压机是现代重型模锻液压机技术发展的结果,具有明显的时代特征,特别是上世纪末本世纪初,预应力坎合重型结构的发明和成功应用,在上世纪小型垂直分模液压机实践的基础上,必将具有数万吨,甚至十万吨的垂直力(V)和水平力(H)的第三液压机和重型挤压筒的设计制造成功,成为我国重型制造领域的世界性创举。
三.熔覆工艺与熔覆-挤压工艺
(1)熔覆工艺LCD和EBAM 简介
熔覆(Cladding)是指,在高能量密度的束流(激光束和电子束)作用下,在材料表面产生的冶金过程,其与3D打印的原理相结合,一层又一层地熔覆(增材成形),即形成LCD——Laser Cladding Diposition(采用大功率激光束)和
EBAM——Electron Beam Additive Manufacturing(采用大功率电子束)工艺,分别见图6和图7。。 LCD和EBAM是重型金属3D打印的首选工艺,原理图见图6A和6b。在LCD喷头中,激光束经透镜被聚焦到熔覆件的表面,形成微熔池,同时金属粉末也同步送到微熔池中,迅速熔化,并随熔池离去而迅速冷却,完成熔池熔覆,连续进行此过程即LCD过程。EBAM过程与此类似,将激光束流换成电子束流、金属粉换成金属丝即可。
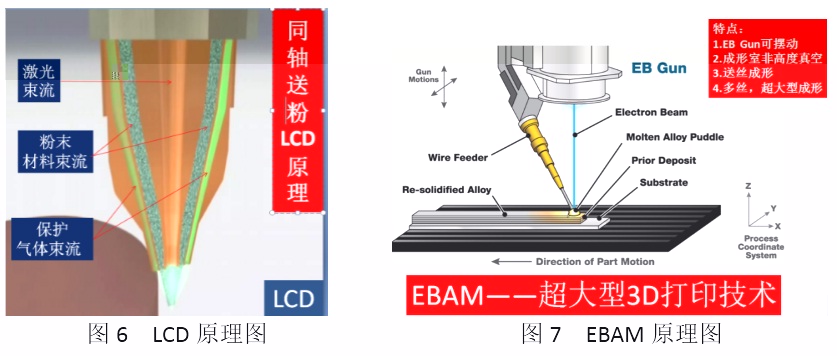
采用LCD和EBAM工艺成形金属构件,特别是重型构件,优点明显:提供熔覆成形的原材料为金属粉末或钢丝,而不是重型高端制造的重型钢锭;熔覆成形过程自动保证了结果的无偏析,而无需重型钢锭的开坯过程;熔覆所得坯件结构形状合理,可最好地满足挤压之需,而不是离挤压要求较远的,粗造的自由锻件。详细分析如下:
A. 熔覆工艺以小型冶炼系统生产的金属粉末或丝材为原材料,而不是以数十吨或数百吨真空冶炼和真空铸锭系统而得的重型钢锭为原材料,这就节省了巨额投资和建设周期,大大降低成本,并节省宝贵的材料;
B.无偏析(Segregation-free),这是以金属粉末和丝材为原材料的3D打印熔覆工艺的共同特点。无数金属粉末在微熔池中迅速熔化并凝固而成形,就从根本上消除了巨大金属熔体凝固(钢锭凝固)之偏析——成分分布不均的严重问题。一切为消除重型钢锭偏析的,复杂而费时的开坯锻造工序均取消。对现代重型模锻和挤压工艺——垂直分模挤压工艺来说,这一优点对极为重要,它为成形件的成分和性能均匀奠定了基础。
B.LCD和EBAM可完复杂的结构的成形工艺,这是垂直分模挤压最佳的制坯工艺,形状合理的,符合挤压工艺需要的坯件,保证垂直分模挤压工艺的顺利进行。图8为美Sciaky公司采用EBAM工艺完成的6米×1.2米×1.2米大型构件照片,图9为我国西北工业大学完成的C919飞机翼肋照片,图10美DM3D公司采用LCD技术完成的大型钛合金构件,图11 美Lasertec公司采用LCD技术完成叶轮。
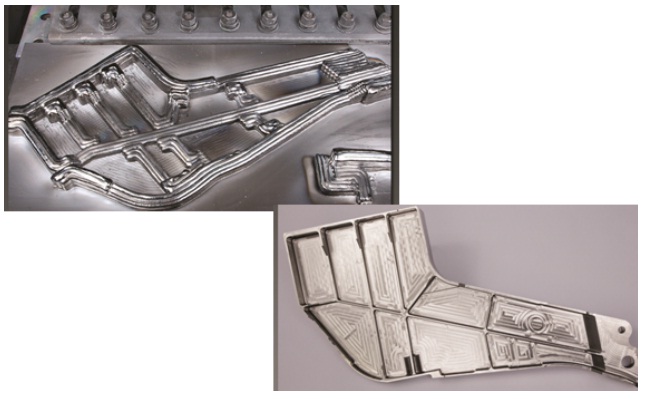
图8 EBAM工艺完成的6米×1.2米×1.2米大型构件,(美Sciaky公司)
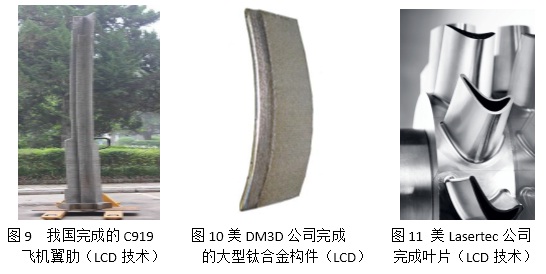
(2)熔覆-挤压工艺
本公司及有关国内外大量的实验证明,LCD和EBAMG工艺完成的结构件之强度,如σ
b(强度极限)和σ
s(流动极限)均可满足工程要求,但有关塑性的指标如δ(延伸率)和ψ(断面收缩率)是不够稳定的,最终影响a
k(冲击韧性)值,常达不到要求。这就是本报告提出的在熔覆成形后,再增加垂直分模挤压的原因。将熔覆——Cladding和挤压——Extrusion结合起来,形成熔覆-挤压工艺——C-E工艺。
C-E工艺是崭新的重型金属成形工艺,它拥有熔覆和挤压两方面的优点,先用熔覆工艺获得优质坯件,再采用垂直分模挤压工艺对,高温金属熔覆坯件施以极其巨大的压应力(σm≈400~500Mpa的球应力),迫使其产生伴随着《动态再结晶》的金属流动而成形,以保证最终制件在强度和塑性两方面,均获的极高的,稳定的机械性能,保证 σ
b、 σ
s、 δ、 ψ 、a
k 全面达标。
四.项目市场分析
以100MN液压机、300MN液压机和1200MN液压机的市场为主线,分别分析市场前景。
100MN液压机产品的市场前景。
该压机是本项目中最小的液压机,投资小,见效快,主要用于压缩天然气瓶、导弹、鱼雷发射管、直升机浆轴等的薄壁、中空、对称和非对称结构件的成形制造。
上述各类均属。目前的先进工艺为管坯旋压,但其成本高,且无法成形非轴对称结构。本项目提出一种以铸锭为原材料的挤压加旋压的导弹制造需工艺,采用铸锭,先采用垂直分模挤压成专用的挤压坯(局部为非对称),再旋压减薄成形。原材料从通用的管材,换改为铸锭材料,成本大大降低;专用挤压,材料利用率提高。
环境污染迫使我们“弃煤从气”、“少油多气”;核电“削峰补谷”技术加快了氢气能的储、运行业的发展;数百万辆的城市燃气的私车和公共车辆等等,助推了大、中、小型气瓶的旺盛需求。然而我国目前的天然气瓶成形制造技术落后,允许内压仅25Mpa,远低于工业先进国家35Mpa的水平。国内、外正在制定65Mpa~70Mpa新标准,这将加大气瓶制造的难度。显然,随着清洁能源的强制推广,各类容/重比(升/公斤)小于0.5~0.7、可靠性高、无爆炸、成本低的气瓶的成形制造,必将成为环境治理中的紧迫问题,天然气瓶是一类重要的,适于100MN压机成形制造的产品。。
石油机械工业需要的大量的厚壁腔体类锻件,现以多向模锻液压机成形为主,显然此类锻件完全可以高效率地在本100MN液压机上制造,如泥浆泵的压缸就是一种比较典型的产品。详见附件1。
300MN液压机产品的市场前景。
该压机属中型垂直分模挤压液压机,是本项目的中坚分项,以大、中型石油腔体锻件:防喷器、泵体、阀体、三通、多通为主。海工储运装备、油气勘探、采掘和防喷装备中的压力壳,以及泥浆泵和页岩气压裂装备的高压部件,由于质量问题造成严重的事故屡见不鲜。英国BP公司在大西洋、太平洋的北海和墨西哥湾的采油平台都发生过严重的事故。为了阻止压力壳深海部件(含管道),由于内、外压应力加快的腐蚀过程,需采用昂贵的30%高镍合金。传统的自由锻、模锻对高镍合金的复杂精化成形,困难很大。多向模锻无法成形大型壳体和腔体。现代海工和油气业的快速发展,正在催生新的腔体和壳体成形工艺。
海工用小型高Ni(30%)管道,以φ247x30x10000为大宗,重量为1750kg,售价为20万/根,这是300MN压机高副加值产品之一。航空锻件:承力框、梁、起落架、涡轮盘等均适合在本压机上锻造成形。详见附件1。
1200MN液压机产品的市场前景。
1200垂直分模挤压液压机是世界最先进的液压机,是我国的创新超重型装备。核电用锻件是该压机的主要产品。我国的能源是关于我国和世界环境的大事。清洁能源中,没有一种能源从规模上能与核电相比。事实上,只有核能的大规模发展,才能迅速改变我国落后的能源结构,改善我国的生态环境。我国已从2011年日本福岛核电站灾难的幽灵中平安走了出来!!!,曾使我国暂停新核电站建设,进行新一轮核安全检查检的3年已过去,我国迎来了核电发展的新时代。核能已成为我国的重要国际“品牌”,是我国经济发展的刺激点 ,是我国国际声望的核心之一,是我国实现多种目标的重要工具。但是,我国核电发展水平还是比较低的,我国的装机容量仅占电力总装机容量的2%。远低于15%世界平均水平,可见市场容量之巨大。
我国引进美西屋公司(WEST HOUSE)AP1000标准,形成我国CAP标准,均禁止纵向(最大主应力引起裂缝的方向)焊缝;管道与壳体、管道与管道均不允许直接以空间焊缝进行连接,空间过渡处必须与本体一体化整体锻造成形。仅此两项标准,就给全世界核锅炉成形制造产业带来前所未有的困难,并导致生产效率极低,材料巨大浪费。本项目的管台和壳台一体化成形技术是解决上述难题的关键技术。如核电主管道(零件7~10吨,1500万/件)以重型3D打印激光熔覆成形的LCD毛坯,代替自由锻坯料(钢锭-开坯-预锻)再通过垂直分模挤压可完成具有中空内径和管台结构的主管道,材料利用率可从20%大大提高到60~70%,制造周期从一年缩短到2个月。70吨重的水室封头(2500万/件),采用本项目垂直分模挤压工艺结合分布挤压工艺(本公司专利),在12万吨垂直分模挤压机上均可以完成。可以说,任何一件目前采用自由锻工艺难以完成的核电锻件,在本项目的1200MN液压机上均可成形制造。详见附件3.
潜艇重型耐压壳体部件也是本1200MN液压机的目标产品之一:外电报导我国潜艇压力壳直径为6米~9米,其耐压壳体部件的成形是潜艇结构设计制造的重点和难点之一,如:如耐压球面舱壁,现有成形技术只能完成少数几种球面舱壁,因而限制了潜艇的总体设计。本项目用于核电压力壳制造的相关成形技术,可移置到潜艇的耐压壳体部件上来,采用垂直分模挤压、分布挤压等先进挤压技术,耐压壳体的制造效率、可靠性等均可期待进一步提高,潜艇总体设计有关方面对本项目多次提出了期望,详见附件2。
国际竞争、封锁与反封锁,不仅表现在尖端技术和成套设备上,不为人知的是,许多表现在重型锻件(如大功率核、火电气轮机和发电机主轴锻件、航空发动机涡轮盘锻件,甚至低速柴油机曲轴锻件还从南韩进口)上。锻件的强度、韧性和抗疲劳性是用于各领域的锻件之共同要求,而高温下的机械性能、抗蠕变性能、耐腐蚀性能、抗冲击性能、低温性能、抗辐射性能等,则不同领域则有不同的要求,这些都是重型锻件生产中必需考虑的,这些方面,在国内外竞争中,表现尤为激烈。
正如前所述,传统的锻压成形工艺已难以满足高端结构件在质、量、节材、节能和成本诸方面的要求。加快研发新的成形制造新技术、新工艺和新设备已成为当务之急。
五.项目简介
项目的核心设备为三台垂直分模挤压机和与4台激光熔覆设备:
重型激光熔覆机, YLC-2型 四台套(图12);
100MN垂直分模挤压(单牌坊结构), YVE-100型液压机,一台套(图13);
300MN垂直分模挤压(双牌坊结构), YVE-300型液压机,一台套(图14);
1200MN垂直分模挤压液压机(四牌坊结构),YVE-1200型液压机,一台套(图15);
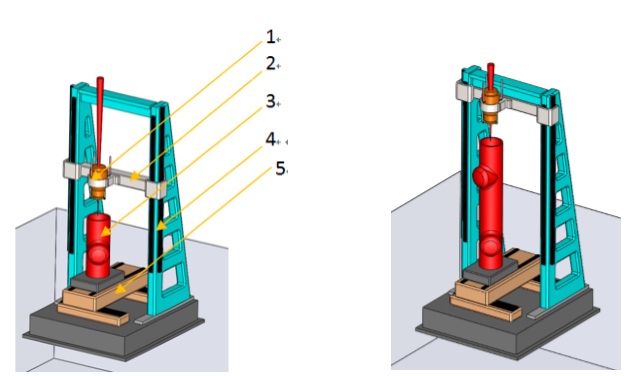
图12 YLC-2图( 1二维喷头2动梁3成形件4导轨5二维工作台)
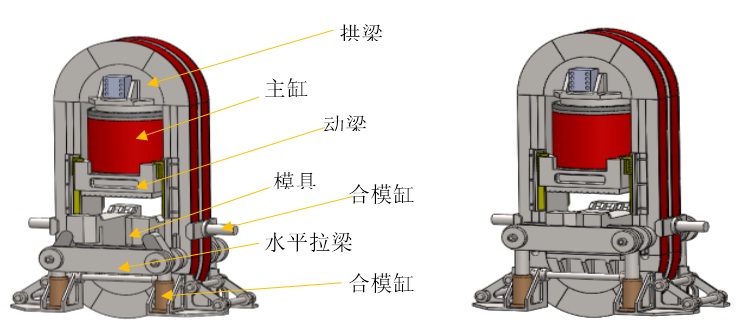
开模状态 闭合状态
图13 100MN垂直分模YVE-100型挤压机
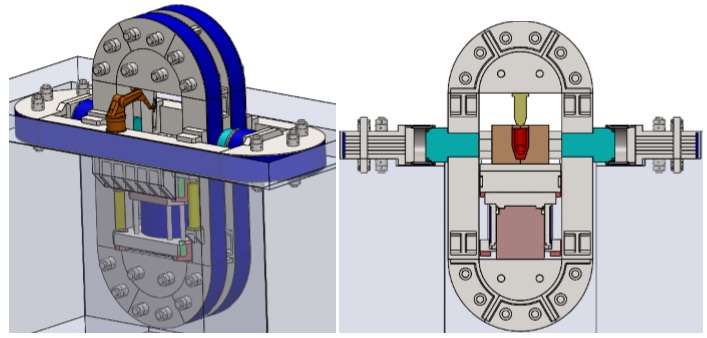
图14 300MN垂直分模YVE-300型挤压机
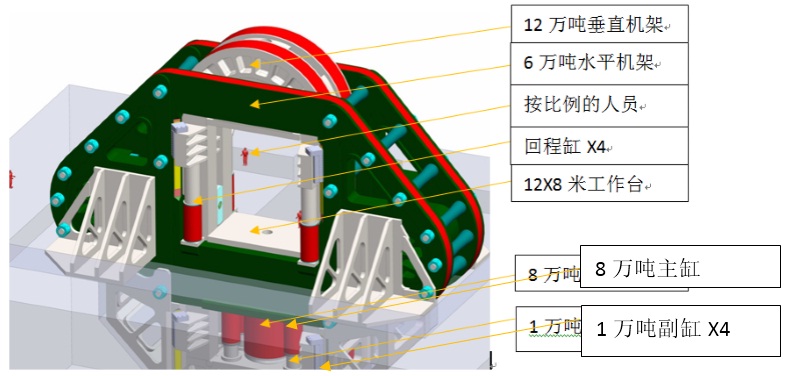
图15 1200MN垂直分模YVE-1200型挤压机设计图
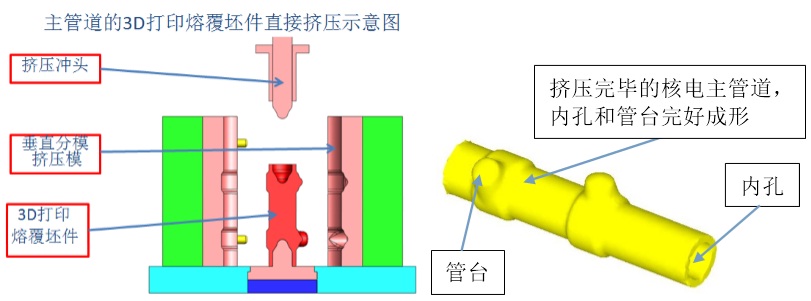
图16 1200MN垂直分模压机上挤压核电主管道示意图
六.项目实施
项目实施采取逐级驱动三步战略:
- 建造重型激光熔覆机YLC-2型4台套,共需2000万,一年投入生产运行;
- 建造一台1万吨YVE-100型垂直分模挤压液压机,需2000万;辅助设备(行车、加热炉、热处理炉等)1500万;厂房(不含土地)2000万;流动资金500万;整个分项目共需6000万投资。一年投产试运行;再加开发市场、培养技术人员和工人时间,整个项目24个月完成。
- 建造一台3万吨YVE-300型垂直分模挤压液压机,需9000万;辅助设备、厂房、流动资金4000万(不含土地),整个分项目共需3亿。 2年投产试运行,再加开发市场、培养技术人员和工人时间,整个分项目36个月完成。
- 建造一台120000吨YVE-1200型垂直分模挤压液压机,5亿;辅助设备、厂房、流动资金(不含土地),1亿,整个分项目共需6亿。2年投产试运行,再加开发市场、培养技术人员和工人时间,整个分项目36个月完成。
整个项目总投资8.1亿元。以上投入为初步计算,根据项目的深入和市场的变化,将可能有小幅调整。
项目进度见表2,项目平面布置图见图17
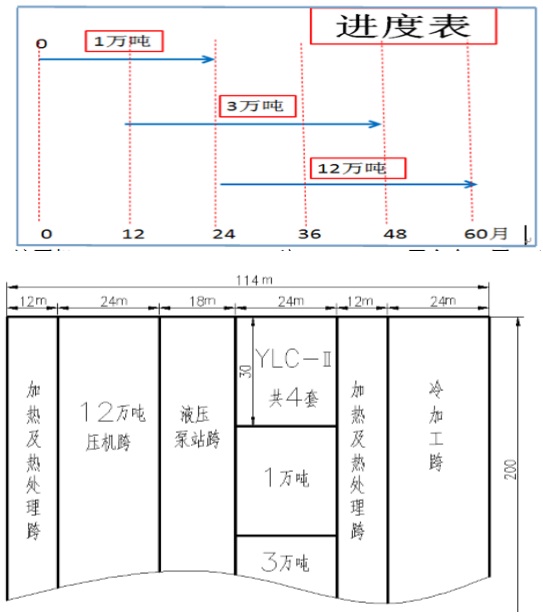
图17 项目平面布置图
七.团队的已有成果
本项目团队(包括清华大学团队)是我国重型液压机创新性最强、完成数量最多、成功率达100%的重型液压机研发、设计、承包制造的团队。
(1)重型锻造行业
始于1984年,团队负责人作为总设计师成功完成和在制的100MN(1万吨)以上的重型或超重型液压机11台
1)1984年,四平100MN板式换热器压机,建成投产,正常运行至今
2)1993年,邯郸300MN板式换热器压机,建成投产,正常运行至今
3)1994年,广州400MN板式换热器压机,建成投产,正常运行至今
4)1995年,兰州200MN板式换热器压机,建成投产,正常运行至今
5)2009年,包头360MN重型钢管垂直挤压机,建成投产,正常运行至今
6)2009年,包头150MN重型镦粗-穿孔液压机,建成投产,正常运行至今
7)2012年,西安航空产业基地400MN液压机,建成投产,正常运行至今
8)2012年,昆山300MN单缸精密模锻液压机,建成投产,正常运行至今
9)2014年,吉林600MN高压液压机,已开始安装,2016.6年底完成
(2)陶瓷机械行业
广东佛山科达和利泰公司与我团队合作,采用我预应力钢丝缠绕技术和规范,共生产4800~7800吨陶瓷砖液压机,从2002~2013年,共生产(含出口)2500台套以上。全国陶瓷机械行业一致高度赞扬我团队的贡献
(3)板式换热器行业
沈阳重锻液压机等公司,与我团队合作,采用我预应力钢丝缠绕技术和规范,共生产6000~20000吨板式换热器液压机,从1984~2013年,共生产(含出口)150台套以上。全国板式换热器行业进口了大量的板式换热器模具,但从未进口一台板式换热器压机。我国钣式换热器行业以板式换热器压机与法、德、瑞典的模具合资。
在30余年间11余台1~6万吨重型模锻和挤压液压机,2500台陶瓷砖成形液压机和钣式换热器液压机的成功研制的基础上,设计了12万吨和3万吨,适于垂直分模挤压的第3代液压机。并通过2次全国评审(2012年4月和2014年4月)。
本项目核心技术拥有完整、自主知识产权,已授权发明专利:6项,已授权实用新型专利:6项,已受理正在审核的专利:6项,具体专利情况如下:
序号 |
名称 |
类别 |
申请日 |
专利号(申请号) |
状态 |
1 |
随动预应力分模挤压系统及方法 |
发明 |
2012.3.8 |
201210059615.2 |
已授权 |
2 |
用于钣式换热器板片压制成形的液压机 |
实用新型 |
2012.4.24 |
201220176998.7 |
已授权 |
3 |
用于钣式换热器板片压制成形的液压机 |
发明 |
2012.4.24 |
201210122054.6 |
已受理 |
4 |
多向承载机架系统 |
实用新型 |
2012.5.21 |
201220227305.2 |
已授权 |
5 |
多向承载机架系统 |
发明 |
2012.5.21 |
201210157840.X |
已受理 |
6 |
反挤压模具 |
实用新型 |
2012.5.10 |
201220206680.9 |
已授权 |
7 |
壳台或管台成形工艺及其所用的反挤压模 |
发明 |
2012.5.10 |
201210142656.8 |
已受理 |
8 |
多段梁 |
实用新型 |
2012.6.20 |
201220290506.7 |
已授权 |
9 |
多段梁 |
发明 |
2012.6.20 |
201210204076.7 |
已受理 |
10 |
垂直分模挤压系统 |
实用新型 |
2012.9.12 |
201220463503.9 |
已授权 |
11 |
垂直分模挤压系统 |
发明 |
2012.9.12 |
201210336214.7 |
已受理 |
12 |
板柱键 |
发明 |
2012.11.29 |
201010103081.X |
已授权 |
13 |
钢壳钢筋混凝土结构件 |
发明 |
2012.11.29 |
201010103085.8 |
已授权 |
14 |
沿母线剖分得组合式重型预应力油缸及其制造方法 |
发明 |
2012.11.29 |
201010197704.4 |
已授权 |
15 |
缸-梁集成系统 |
实用新型 |
2012.12.17 |
201220697018.8 |
已授权 |
16 |
缸-梁集成系统 |
发明 |
2012.12.17 |
201210547854.2 |
已受理 |
17 |
分布挤压工艺方法及其分布挤压模具 |
发明 |
2009.06.17 |
ZL200910032470.5 |
已授权 |
18 |
高压气瓶 |
发明 |
2010.10.27 |
201010270692.3 |
已授权 |
2011年2月20日胡锦涛书记主席于清华大学,2012年6月19日习近平副书记主席于清华大学接见清华团队负责人颜永年,见图18和图19。
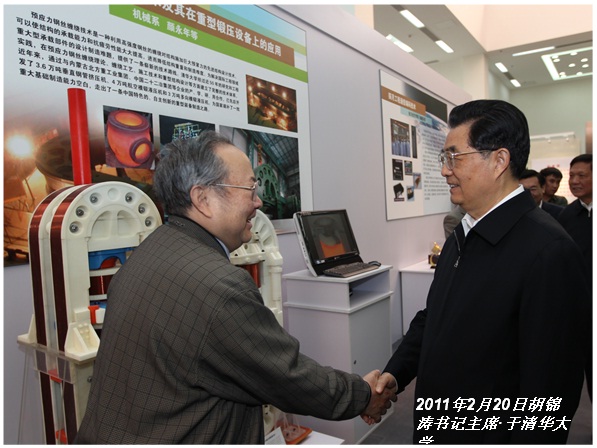
图18胡锦涛书记主席接见颜永年照片
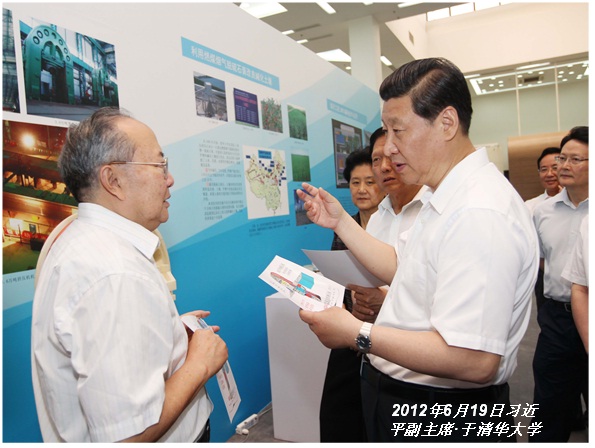
图18习近平副书记主席接见颜永年照片
八.附件1(100MN和300MN液压机的主要产品)
本附件列举了军工类、电站类、气瓶类、航空类、石化类、矿山机械类、高压容器、汽车类、船机类共九大类39种高端锻件的材料、工艺特点、重量、价格等属性,这是100MN和300MN垂直分模液压机可以完成的高端锻件的一部分,仅管不全,但已可看出本项目的重大意义。
一.军工类锻件
类别 |
军工锻件 |
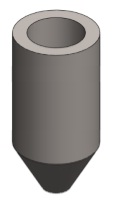 |
名称 |
鱼雷外壳、导弹部件 |
材质 |
钛合金 |
重量 |
|
轮廓尺寸 |
|
锻件价格 |
|
工艺特点 |
薄壁件,挤压一体成型,机加工; |
二:电站类
类别 |
电站锻件 |
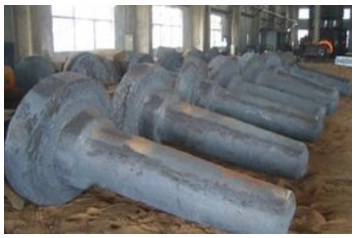 |
名称 |
风电轴、法兰盘 |
材质 |
AISI410 |
重量 |
多种规格 |
轮廓尺寸 |
φ1500以内 |
锻件价格 |
≈10-80万 |
工艺特点 |
闭式挤压成型,机加工 |
类别 |
电站锻件 |
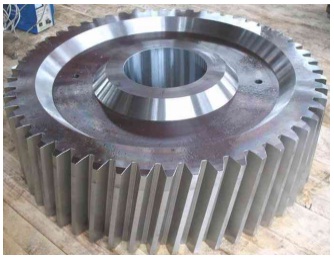 |
名称 |
风电、水电、火电锻件 |
材质 |
AISI410 |
重量 |
多种规格 |
轮廓尺寸 |
φ1500以内 |
锻件价格 |
≈5-15万 |
工艺特点 |
闭式挤压成型,机加工; |
类别 |
电站锻件 |
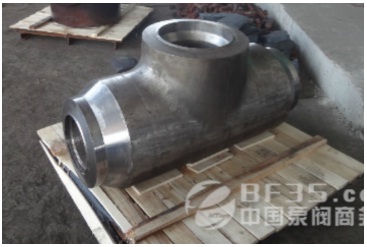 |
名称 |
火电用阀门 |
材质 |
AISI4130 |
重量 |
多种规格 |
轮廓尺寸 |
多种规格 |
锻件价格 |
≈2-18万 |
工艺特点 |
垂直分模,水平穿孔,挤压成型,机加工; |
|
|
|
|
三:气瓶类
类别 |
容器类锻件 |
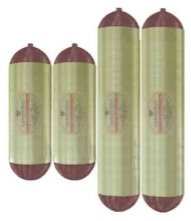 |
名称 |
天然气运输气瓶 |
材质 |
铝合金、不锈钢等 |
重量 |
多种规格 |
轮廓尺寸 |
φ1000以内 |
锻件价格 |
≈2-10万 |
工艺特点 |
垂直分模,挤压成型,模具收口,机加工,外面钢丝缠绕; |
四:航空类
类别 |
航空锻件 |
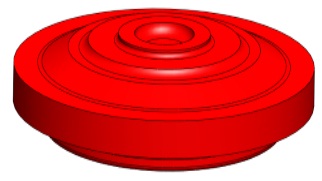 |
名称 |
直升机涡轮盘 |
材质 |
高温合金 |
重量 |
|
轮廓尺寸 |
多种规格 |
锻件价格 |
≈10-50万 |
工艺特点 |
闭式挤压成型,机加工; |
类别 |
航空锻件 |
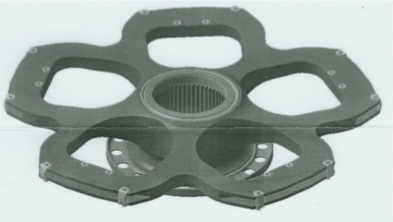 |
名称 |
直升机主桨毂 |
材质 |
钛合金Ti-1023 |
重量 |
171Kg |
轮廓尺寸 |
φ800x250 |
锻件价格 |
≈10万 |
工艺特点 |
锻造,一体成型,机加工; |
|
|
|
|
|
五:石化类
类别 |
石化锻件 |
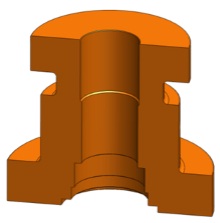 |
名称 |
套管头、管道、三通、法兰等 |
材质 |
AISI-410 |
重量 |
600Kg |
轮廓尺寸 |
φ350xφ500x900 |
锻件价格 |
≈1.5万 |
工艺特点 |
垂直分模,挤压成型,机加工; |
六:矿山机械类
类别 |
矿山机械锻件 |
 |
名称 |
十字轴等 |
材质 |
40Cr、40CrNi、20CrMo等 |
重量 |
3.5吨 |
轮廓尺寸 |
多种规格 |
锻件价格 |
≈7.5万 |
工艺特点 |
闭式锻造,机加工; |
七:高压容器
类别 |
高压容器锻件 |
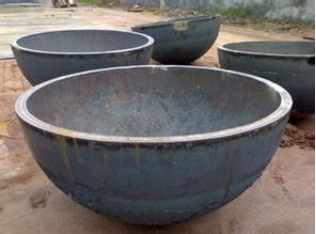 |
名称 |
球形封头 |
材质 |
AISI-410 |
重量 |
多种规格 |
轮廓尺寸 |
φ1200以内 |
锻件价格 |
≈5-85万 |
工艺特点 |
垂直分模,压边拉深挤压成型,局部机加工; |
类别 |
高压容器锻件 |
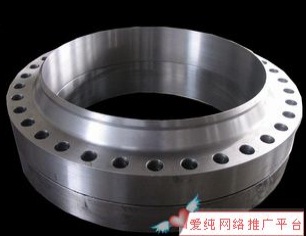 |
名称 |
压力容器法兰 |
材质 |
AISI-410 |
重量 |
多种规格 |
轮廓尺寸 |
φ300至φ1500 |
锻件价格 |
≈3-70万 |
工艺特点 |
挤压成型,机加工; |
八:交通类
类别 |
汽车锻件 |
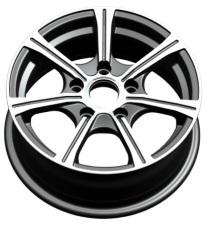 |
名称 |
锻造轮毂 |
材质 |
铝合金 |
重量 |
|
轮廓尺寸 |
多种规格 |
锻件价格 |
≈0.2万 |
工艺特点 |
闭式挤压成型,机加工 |
类别 |
汽车锻件 |
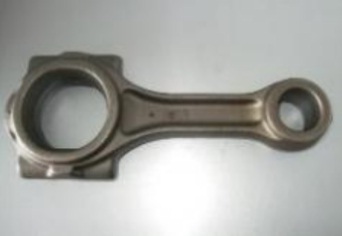 |
名称 |
锻造连杆 |
材质 |
35CrMo |
重量 |
多种规格 |
轮廓尺寸 |
汽车、卡车等 |
锻件价格 |
≈0.08-0.2万 |
工艺特点 |
整体锻造成型,局部机加工; |
类别 |
船用锻件 |
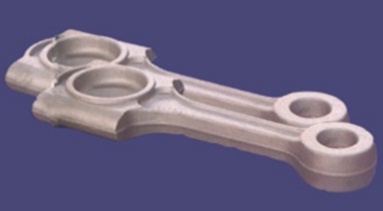 |
名称 |
船用中型连杆 |
材质 |
35CrMo |
重量 |
多种规格 |
轮廓尺寸 |
多种规格 |
锻件价格 |
≈0.5-5万 |
工艺特点 |
整体锻造成型,局部机加工; |
九.附件2(1200MN液压机主要产品)
本附录列举了军工类、电站类、航空类、石化类、
汽轮机类、高压容器、
船机类、轨道交通类共八大类42种高端锻件的材料、工艺特点、重量、价格等属性,这是12万吨液压机可以完成的高端锻件的一部分,仅管不全,但已可看出本项目的重大意义。
一:军工类锻件
类别 |
潜艇部件 |
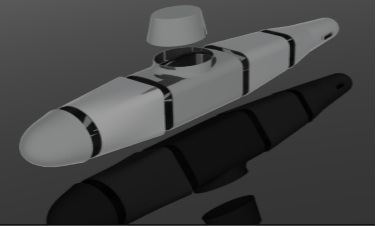 |
名称 |
潜艇外壳 |
材质 |
980钢 |
重量 |
|
轮廓尺寸 |
|
锻件价格 |
|
工艺特点 |
采用垂直分模挤压,优化原结构设计,部分零件采用整体成型; |
类别 |
军工锻件 |
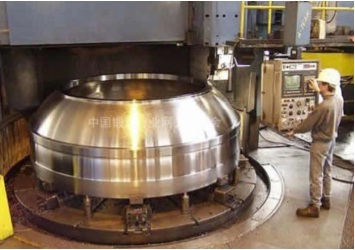 |
名称 |
火箭推进器顶盖 |
材质 |
德国萨尔锻造厂 |
重量 |
|
轮廓尺寸 |
|
锻件价格 |
|
工艺特点 |
智能工具锻造 |
类别 |
军工锻件 |
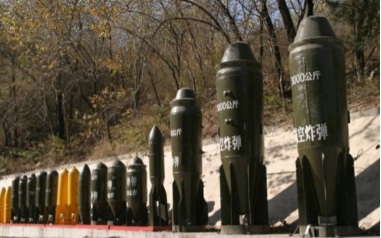 |
名称 |
反坦克导弹壳体 |
材质 |
|
重量 |
|
轮廓尺寸 |
|
锻件价格 |
|
工艺特点 |
挤压成型,机加工; |
二:电站类
类别 |
核电锻件 |
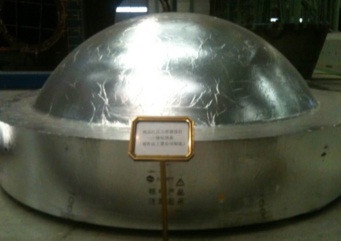 |
名称 |
AP1000压力容器顶盖、以及主管道等 |
材质 |
A508-Ⅲ |
重量 |
58吨 |
轮廓尺寸 |
φ4650x4300 |
锻件价格 |
|
工艺特点 |
垂直分模,分布挤压成型,机加工; |
类别 |
核电锻件 |
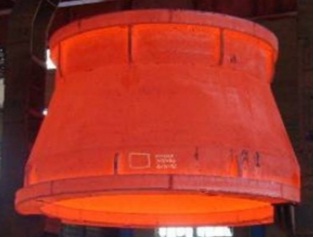 |
名称 |
CPR1000锥型筒体 |
材质 |
A508-Ⅲ |
重量 |
160吨 |
轮廓尺寸 |
φ4850x8200 |
锻件价格 |
|
工艺特点 |
初步挤压成型,智能工具锻造成型,机加工; |
类别 |
核电锻件 |
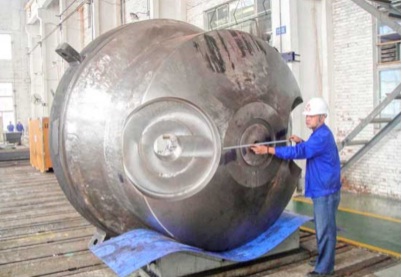 |
名称 |
AP1000稳压器下封头 |
材质 |
A508-Ⅲ |
重量 |
160吨 |
轮廓尺寸 |
φ4650x6200 |
锻件价格 |
|
工艺特点 |
垂直分模,分布挤压成型,机 |
类别 |
核电锻件 |
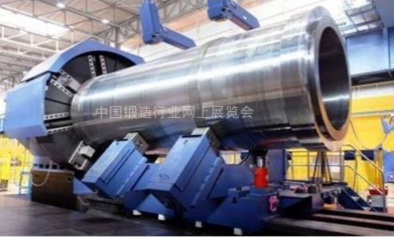 |
名称 |
核废料储罐外壳 |
材质 |
A508-Ⅲ |
重量 |
|
轮廓尺寸 |
|
锻件价格 |
|
工艺特点 |
初步挤压成型,水平智能工具锻造成型,机加工; |
类别 |
核电锻件 |
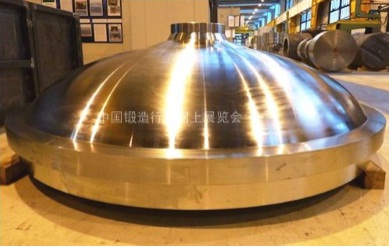 |
名称 |
核废料储罐下封头 |
材质 |
A508-Ⅲ |
重量 |
|
轮廓尺寸 |
|
锻件价格 |
|
工艺特点 |
分布挤压成型,机加工; |
类别 |
水电锻件 |
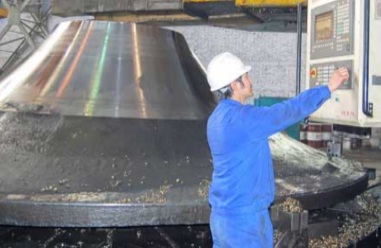 |
名称 |
水电上冠 |
材质 |
CrMo钢 |
重量 |
50吨 |
轮廓尺寸 |
φ4800x2050 |
锻件价格 |
≈150万 |
工艺特点 |
初步挤压成型,智能工具锻造成型,机加工; |
类别 |
水电锻件 |
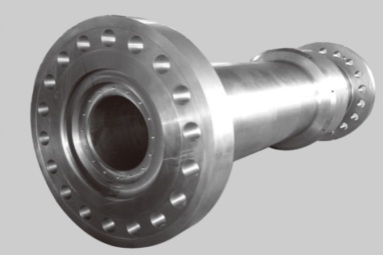 |
名称 |
大型水电电机主轴 |
材质 |
CrMo钢 |
重量 |
43吨 |
轮廓尺寸 |
φ1800x3500 |
锻件价格 |
≈120万 |
工艺特点 |
初步挤压成型,智能工具锻造成型,机加工;
|
三:航空类
类别 |
航空锻件 |
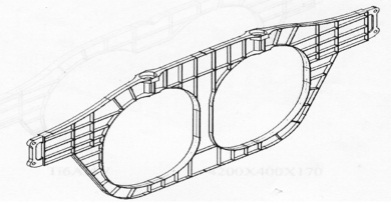 |
名称 |
第四代机15918框 |
材质 |
钛合金TI-6AL-4V |
重量 |
865Kg |
轮廓尺寸 |
3900x1750x110 |
锻件价格 |
≈18万 |
工艺特点 |
闭式锻造,一体成型,机加工; |
类别 |
航空锻件 |
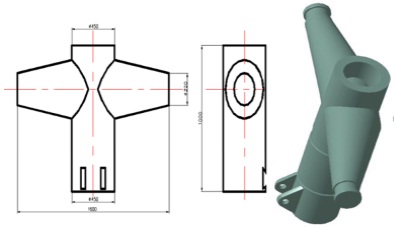 |
名称 |
大运起落架 |
材质 |
300M |
重量 |
3000Kg |
轮廓尺寸 |
1600X1100X450 |
锻件价格 |
≈30万 |
工艺特点 |
垂直分模,挤压成型,机加工; |
类别 |
航空锻件 |
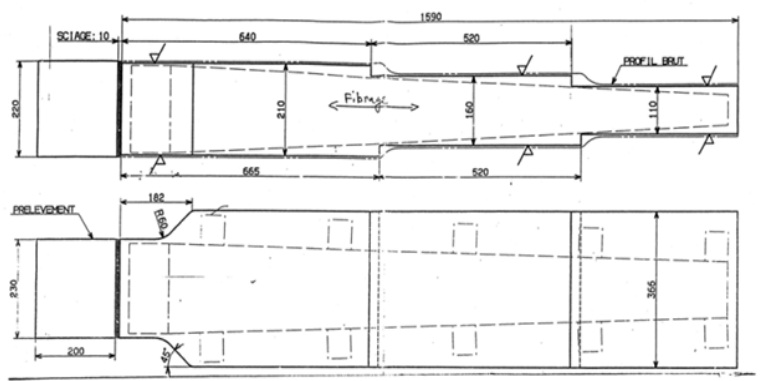 |
名称 |
超七飞机主梁锻件 |
材质 |
高强钢PH13-8Mo |
重量 |
800Kg |
轮廓尺寸 |
1590X366X320 |
锻件价格 |
≈10万 |
工艺特点 |
闭式锻造,一体成型,机加工; |
类别 |
航空锻件 |
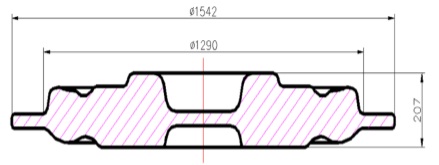 |
名称 |
GT25000海军舰用燃机第5、6级涡轮盘 |
材质 |
GH698 |
重量 |
1904Kg |
轮廓尺寸 |
φ1542x207 |
锻件价格 |
≈20万 |
工艺特点 |
3D打印制坯,闭式镦挤压成型,机加工; |
类别 |
航空锻件 |
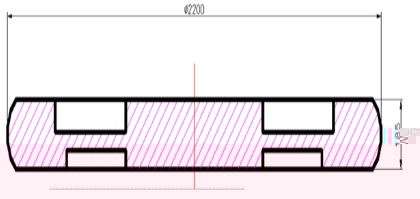 |
名称 |
R0110重型燃机2级涡轮盘 |
材质 |
GH2132 |
重量 |
3961Kg |
轮廓尺寸 |
φ2200x185 |
锻件价格 |
≈80万 |
工艺特点 |
3D打印制坯,闭式镦挤压成型,机加工; |
类别 |
航空锻件 |
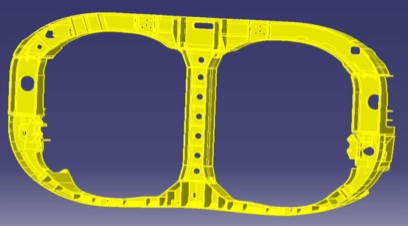 |
名称 |
大运机身整体框 |
材质 |
钛合金TI-6AL-4V |
重量 |
1868Kg |
轮廓尺寸 |
2600x4260x256 |
锻件价格 |
≈50万 |
工艺特点 |
闭式锻造,一体成型,机加工; |
四:石化类
类别 |
石化锻件 |
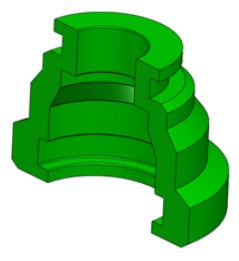 |
名称 |
壳体 |
材质 |
AISI-410 |
重量 |
16吨 |
轮廓尺寸 |
φ2120xφ694x1515 |
锻件价格 |
≈45万 |
工艺特点 |
垂直分模,挤压成型,机加工; |
五:汽轮机类
类别 |
蒸汽轮机锻件 |
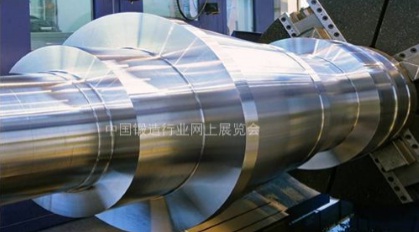 |
名称 |
蒸汽轮机用轴件 |
材质 |
|
重量 |
|
轮廓尺寸 |
|
锻件价格 |
≈200-400万 |
工艺特点 |
垂直分模,挤压成型,智能工具锻造,机加工; |
类别 |
蒸汽轮机锻件 |
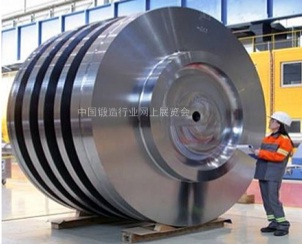 |
名称 |
蒸汽轮机用轮盘 |
材质 |
|
重量 |
|
轮廓尺寸 |
|
锻件价格 |
≈200-400万 |
工艺特点 |
垂直分模,挤压成型,机加工; |
六:高压容器
类别 |
高压容器锻件 |
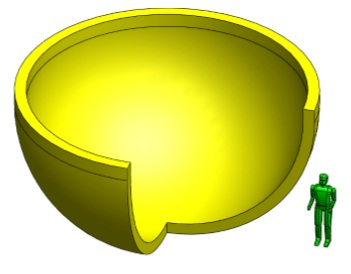 |
名称 |
球形封头 |
材质 |
AISI-410 |
重量 |
54.5吨 |
轮廓尺寸 |
φ6500xφ6300x3500多种规格 |
锻件价格 |
≈150万 |
工艺特点 |
压边拉升挤压成型,局部机加工; |
七:船机
类别 |
船机锻件 |
 |
名称 |
大型曲轴 |
材质 |
45# |
重量 |
280吨 |
轮廓尺寸 |
10000 |
锻件价格 |
≈800-1000万 |
工艺特点 |
智能工具,局部锻造,机加工; |
八:轨道交通类
类别 |
轨道交通锻件 |
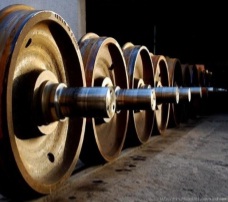 |
名称 |
火车轮对 |
材质 |
R7钢 |
重量 |
|
轮廓尺寸 |
多种规格 |
锻件价格 |
≈10-15万 |
工艺特点 |
闭式挤压成型,机加工 |